FREQUENTLY
ASKED QUESTIONS
There are three main stages to stormwater treatment and management. All three systems when combined from a complex but efficient treatment system that is able to remove almost all contaminants and pollutants, both physical or dissolved. the first stage is the primary treatment stage. This stage incorporates the removal of larger debris and trash and its usually seen as a gross pollutant trap. This stage is the vital part of the process as it is the first line of defense for the stormwater management system with the larger more damaging pollutants being remove as this point. These system mainly focus on the physical process of filtration such a physical screening, hydrodynamic separation and sedimentations. This primary process is designed to increase the longevity of the system, reducing maintenance frequency, reducing sediments load and maintaining steady flow of water.
The second stage in the treatment process is the secondary treatment stage. This stage is mainly focus on attempting to achieve the certain degree of effluent quality by using process to remove fine particles sedimentations, setting chambers and oil removal. These pollutants that are removed are all typically classified as non-attached pollutants such as sediments and oils. The most commonly used systems that are seen as secondary treatments systems is the oil separator and coalescing systems.
The final step in the stormwater management system is the tertiary treatment systems. These system are usually classified by enhanced sedimentation and filtration, biological update , adsorption and chemical filtration process. The pollutants that are usually aimed to be removed are nutrients, heavy metals and phosphorous, attached particles and bacteria. These system are usually more complex, using a range of media using a variety of chemicals processes to remove miniscule particles and attached pollutants. This secondary treatment process. After this final treatment process is completed and the desired pollutants levels are achieved the water is returned to the environment, to water storage or retentions basins.
· Physical Local and Rainfall Conditions determine the size of inlet, the bypass size and the tank capacity
· Catchment Size usually define the size of the physical trap as well as the silt containment chamber and capacity
· Typical Contaminant Types and Gross pollutants determine the trap size as well as
· Human Foot Traffic
· Site Flow Rate to determine the required size of the inlet, bypass and the overall capacity
· Risk Analysis
These considerations are usually taken when determining the best size of Gross pollutant trap. Our ECOPROTECTOR comes in a wide range of sizes, each with varying inlet options, capacities and pollutant capture amounts. For information of the common ranges of sizes that are supplied and assistance with the best sized system for your site demands please visit www.protector.com.au
They are able to use gravity separation processes to capture oil if it is present as a dissolved pollutant. Using the simple process of gravity separation, once the stormwater enters the silt chamber and settles, the oil rises to the top of the stormwater and separates due to the density differences. Due to the placement of the outlet riser, the oil is unable to rise out of the outlet and is trapped. This oil can be removed through vacuum truck maintenance removal.
The infiltration of large debris and gross pollutants into our water ecosystems can cause irreversible damage. Sea life and marine fauna can mistake trash and debris from food, or be caught in plastic waste products and cause the death of a large amount of marine life. The important role that gross pollutant traps play in our stormwater treatment systems cannot be over sold as the protection of our environment can never be overlooked.
In terms of the need for gross pollutant traps in treatment train systems and stormwater management processes the gross pollutant traps provide an abundance of advantages. They are a necessary part of the treatment train as they are proven to reduce the likelihood of blockages and restriction of water flow into the further treatment systems to allow for complete efficient operation. Furthermore they reduce the maintenance frequency of tertiary and secondary treatment systems allowing more complete operation for longer periods of time. Gross pollutant traps are also proven to reduce the sediment load imparted onto tertiary treatment and biological treatment system and increasing the longevity of the biological treatment processes and the filtration media used in tertiary systems.
If it is required to have a complete treatment system that has a long lifespan ad effectively removes all forms of pollutants, a gross pollutant trap is a necessity.
As previously stated, any form of weather conditions outside the norm of which the specific GROSS POLLUTANT TRAP is design fall, be it high rainfall or heavy storm conditions, an immediate inspection is recommended.
NB: when maintenance is conducted on the GROSS POLLUTANT TRAP system, ensure that all Workplace health and Safety precautions and directions are adhered to and the Confined space Regulations are carefully followed when required.
The cleaning and maintenance procedure is simple, requiring removal of the access cover and inserting a suction hose into the chamber, recommended use of a vacuum loader truck. Remove all forms of refuse and debris before entering the chamber. Always ensure cleaning is begun from the inlet side of the chamber and ensure carefully rescuing of the access cover when completed.
Specific maintenance procedures of each aspect of the stormwater treatment system is outlined below. All maintenance must be carried out by some authorized personnel and all OH and S regulations and confined space regulations must be strictly followed.
Chamber Maintenance
1. Remove access manway carefully and safely.
2. Using a vacuum or hose truck, insert a suction hose into the chamber. Remove all forms of refuse, silt and debris before entering the chamber. Always ensure cleaning is begun from the inlet side of the chamber and ensure carefully rescuring of the access cover when completed.
Interior Maintenance
1. Gross Collector – Remove all sediment, gross pollutants and anything other trash that can restrict water flow.
2. Trash screen – ensure that all clogging is removed, and that water can flow without obstacle through the trash screen
3. Bypass channel – clean out all sediment that may have entered the bypass.
4. Dropper pipe and Riser Tube – ensure clogging has not occurred and that free flow is possible.
5. Silt Chamber – Use that vacuum truck and hose to remove all sedimentation at the bottom of the GROSS POLLUTANT TRAP.
Gravity Separation – This principle works off a simple theorem, Stokes Law. This defines that the buoyant velocity rise of a droplet is greatest when the density of the droplet, in this case oil, is greater than the density of the continuous phase, the water. This hence means that oil particles and hydrocarbons will always rise to the surface of water. Hence this process can be used to separate the hydrocarbons from water in a non-turbulent flow, such as in a storage or retention system.
· Coalescence – In water treatment, the energy that is input into water is very low, causing the process of coalescence to occur in what small oil droplets collide and form bigger droplets, and due to the low energy these particles do not disperse. This process allows for the particles to be removed more simply.
· Adsorption – This process is the adhesion of atoms, ions or molecules (such as hydrocarbons) to a surface. This is a surface phenomenon in which the hydrocarbons will attach themselves to the surface of another system (such as the filter systems) and hence be removed from the flow of water.
In reality a combination of these processes is the best process for the removal of hydrocarbons from stormwater. Systems that encapsulate these are the greatest for hydrocarbon removal and management.
We at PROTECTOR have a wide range of solutions for the removal of hydrocarbons from stormwater. We have two types of oil separator systems, both of which suit various sit demands and settings. The is our Highly efficient, full retention separator to treat first flush, fine particulates, nutrients, heavy metals and hydrocarbon filtration system and the Dual chamber, fine particle, sedimentation and organic pollutant removal treatment with large retention and Bypass.
Adsorption – Adsorption is the most common and simplest process and is the adhesion of ions or molecules to the surface of the absorbent, with this layer then being removed through maintenance or filter replacement.
Chemical precipitation – The most common form of chemical precipitation to remove Zinc is through the use of insoluble hydroxide salt. The salt is formed by the adjustment of pH to roughly 10 level and this salt cause the Zinc to attach and create an insoluble substance that is considered a solid, allowing the simpler removal of the zinc. The system must be allowed to settle for the precipitation to occur making this process more difficult to occur.
Solvent extraction – The use of solvent exchange to remove metals and water from industrial wastewater is a common process to achieve regulated Zinc levels.
Ion exchange – this process can be used to remove zinc from stormwater. Ion exchange systems can be designed to treat zinc by forcing the water through cation and anion resin beds along with activated carbon to produce deionized water. This process essentially causes an exchange of ions and causing the replacement of these ions with similarly charged ions of which are not considered pollutants in stormwater. Since Zinc ions are positively charged, a cation exchange process is used to exchange the positively charged ion with that of what is available on the surface of the resin or the media. This process can also be known as water softening.
We have a range of tertiary treatment systems that incorporate these chemical filtration processes. Our XTREAMPROTECTOR, , and MAXIPROTECTOR all incorporate a range of zeolite, activated carbons, AFM, perlite, and various other filter media. Our utilizes biofiltration to remove these products through microorganism biodegradation. We have all the solutions for your tertiary treatment needs.
Storm water is water that is produced from rain, and possibly melting snow and ice, which flows over solid surfaces, capturing gross pollutants, sedimentation, nutrients, heavy metals and a wide range of other pollutants. The majority of this water infiltrates into the soil, or evaporated or run off and enter nearby waterways. In natural areas, free from construction, buildings, motorways and agriculture etc. the water just soaks and absorbs into the soil or evaporates. In developed areas, not only does the range and concentrations of pollutants grow and grow, but the areas in which the water is usually absorbed or evaporated is removed, the storm water is funneled through stormwater drainage systems and directly into our rivers, streams and waterways. The natural processes of stormwater removal such as infiltration evaporation and filtering are greatly reduced, causing the concentrations and size of pollutants entering our waterways to drastically increase.
Stormwater treatment and management is about protecting our environment. When we develop stormwater treatment systems we are designing ways in which to protect our environment, and rid our environment and ecosystems of pollution and contamination. Hence the need for these systems is vital for our environment and ecosystems health and prolonged life. From gross pollutant traps which remove larger plastics, debris and sedimentation from our waterways, keeping our oceanic and water ecosystems protected from the well-known dangers of ocean and marine life coming into contact with plastics, to our tertiary treatments to remove heavy metals, organic nutrients and colloidal fine particles from our water systems and prevent from poisoning the environment. If the management of stormwater is conducted properly, with effective and efficient technologies in place, we can improve our water ecosystems and effectively lengthen our environments life.
Not only does proper stormwater treatment and management protect our environment, it also has several other benefits that are less widely known. These management systems can reduce flooding to protect people’s lives and properties, reduce the demand on public stormwater drainage systems, support healthy streams and rivers, and create healthier, more sustainable and viable communities. Effective stormwater management provides not only vital environmental benefits, it also provides social, economic and communal benefits.
It’s important in society to maintain a clear image of the bigger picture. As our society continues to grow in population and city size, we increase the area covered by impervious and non –absorbent surfaces that do not allow infiltration and absorption and in turn increase the amount of polluted runoff. We must continue to implement these stormwater treatment technologies not for just the current benefit, but also for the future and more vital benefits.
So it is a Big Deal. It is Important, it is vital, it is necessary. Stormwater treatment and management is a must as we continue to develop and grow.
Written by Nathan D. Raco, in partnership with Protector–Stormwater management Solutions
https://www.protector.com.au
When considering what are the best processes for treating stormwater runoff in a certain application, it is vital to consider the various forms of contaminants that are produced in these areas, as well as the environment in which the application is to be placed in. Carpark developments have the tendency for high levels of oils, gross pollutants from high foot traffic, hydrocarbons and heavy metals produced from cars and rooftops. These areas need to be thoroughly treated for discharge back into the environment, as usually is the requirement for water treatment in these areas. Hence the tertiary treatment systems in conjunction with gross pollutant traps are required for these areas, with all of the protector tertiary designed systems removing the required contaminants that are produced from these areas.
The processes best used for carparks as their applications include:
- Gross Pollutant traps
- Gravity separation
- Coalescence
- Adsorptions
- Attachment and interception
- Sedimentation
- Precipitation
There isn’t one single process that best removes a certain contaminant. To best tackle the removal of pollutants, a wide range of techniques need to be used in conjunction with each other to ensure the most effective removal possible. High traffic areas have a series of pollutants that remain a big issue in treatment of these systems. High traffic areas produce contaminants such as high amounts of hydrocarbons, high levels of gross pollutants, heavy metals and fine sedimentation. Hence solutions are required to remove these pollutants are produce water for the environment with as low percentages as possible. Hence a combination of primary, secondary and tertiary, and depending on the weather conditions and flow rates of the area, retention systems.
The processes which we recommend to be utilized in the removal of pollutants produced from highways include:
· Gross Pollutant traps
· Gravity separation
· Coalescence
· Adsorptions
· Attachment and interception
· Sedimentation
Biofiltration is the disintegration of materials through bacteria, fungi or other biological means. Essentially the process of biodegradation is in which material is consumed by microorganisms. This process can be implemented effectively in stormwater treatment, in conjunction with soil. Due to soils high absorbance, water is absorbed into the soil media in which these bacteria and microorganisms live, and the contaminants are slowed in the soil and are hence consumed by the organisms living in the soil. The water flows out of the soil with contaminants removed. These microorganisms in fact use this process to increase their population and remove the contaminants more efficiently. The matter which is able to be consumed by these microorganisms are generally organic materials such as hydrocarbons and nutrients.
Our BIOPROTECTOR is our biofiltration system, on of the most advanced on the market. It utilizes both physical and biofiltration systems to ensure maximum contaminant removal.
· Zeolite – Zeolite is a microporous, aluminosilicate mineral commonly used as an adsorbent and catalytic material. Zeolite occurs naturally but is also easily manufactured on an industrial scale and is hence one of the larger adsorption materials available. Zeolites have a porous structure that can accommodate a wide variety of cations such as sodium’s, potassium’s and magnesium’s and hence are highly reactive to remove chemicals from waterways. It is also a powerful remover of:
· soluble metals
· nutrients
· organic material
· Activated Carbon – Activated carbon is commonly used to adsorb natural organic compounds, as well as even taste and smell compounds, in water treatment processes. It is a highly effect filtration media because it is a highly porous material and provides a large surface area to adsorb contaminants. Through the adsorption process, a both physical and chemical process of accumulating a substance at the interface between liquid and solid phases, this organic filter media is able to efficiently remove oil and grease as well as organics such as PAHs and phthalates.
· Organic material
· Nutrients
· Oil and grease
· Perlite – This substance is an amorphous volcanic glass or ash that has a high-water content and is formed by the hydration of obsidian. It also has the unique of a high expansion rate when heated and when this is done the production of perlite filter aids occurs. These aids have a jagged, interlocking structure with a myriad of microscopic channels which still allow reasonable flow rates with a high total phosphorus removal ratio. It is able to adsorb dissolved-P and filtering particulate-P simultaneously due to its structure and it is able to effectively remove:
· Sedimentation and total suspended solids
· Oil and grease
· Nutrients
· Phosphorus
· Soluble Metals
· Total Phosphorus
· Activated Filter Media – Activated filter media is a filtration media that is designed as a filtration replacement for sand by doubling the performance of regular sand filters. AFM is a media that is engineered as a product of a specific glass type, processed to obtain the optimum particle size and shape, and then processed in a 3 step activation process to increase the surface area by up to 300 times its original size to ensure superior filtration. The AFM media also resists filter issues such as biodynamic instability, resists transient wormhole channeling and doesn’t require recharging or replacement. It also lowers backwash demand by roughly 50% as well as having a lifespan that mirrors the filter system in which it is present in.
· Biological Media – this material is considered to be anything that is inert that provides an ecosystem for particular bacteria to exist and reproduce in that are desired to break down these toxic pollutants into a less toxic form. If the media is right, specifically temperature above 13 degrees, ammonia and nitrite as food and the existence of oxygen the bio load increase and the bacteria reproduce. This bacteria breaks down the pollutants into a less toxic form and is then able to be removed and the water produced is much cleaner to be returned to the environment.
· Ion Exchange Resins – Resins are a less used filter media, and work by attracting a specific molecule to adhere to them. These resins can either be a cation and anion material and attract the ions to be removed causing the replacement of these ions with similarly charged ions of which are not considered pollutants in storm water.
In combination, these filtration media types can form an effective filtration rate and remove a large number of contaminants. If the combination of these types of filtration media occur, we have the efficient removal of:
· Sediments and Total suspended solids
· Oils and Grease
· Soluble Metals
· Organic Materials
· Nutrients
· Total Phosphorus
Several things are vital in the construction of an effective and efficient stormwater treatment system. Firstly, the system needs to encapsulate all process required for the site in which the runoff is being produced. This means careful considerations of the surrounding environment and its specifications which include:
· Physical Locale
· Rainfall conditions
· Surrounding environment, be it man made or natural
· Catchment size
· Contaminant types
· Flow rate
· Risk analysis.
Once these considerations are reviewed, we can effectively determine which processes need to be used to remove the contaminants that shall be produced. From this it can be decided which systems must be installed, whether it be a single or a complex treatment train. It must be also ensured that no unnecessary systems are implemented which will provide no significant assistance to the stormwater treatment process. If all of the contaminants that can be present are considered, the correct processes can be implemented to ensure effective removal before the water is returned to our waterways and ecosystems.
It is vital that only proven well tested processes are used in the treatment processes. This means that the process in which are being implemented must all be proven and ensured to be THE MOST effective and efficient in our processes. This is why there is constant need for redevelopment and research into the stormwater treatment technologies so that we are constantly improving the processes in which we currently use.
The main reason in which Fibre reinforced polymers are such a useful material as it is considered a composite material, which are materials that are the result of from bonding two or more homogenous materials to derive a final material with specific required physical, mechanical and chemical properties. Currently, they have a high potential to replace conventional materials such as steel and concrete in these infrastructure systems due to their amazing high strength and stiffness, greater fatigue strength and energy absorption capacity and corrosion resistance among other advantages.
Usually the matrix system , or the binding agent, is the plastic material. The matrix is a strong but relatively weak system that has undesirable mechanical properties when considered in an application that requires long life, high strength and corrosion resistance. These systems are brittle, with low durability, deform easily under load and have a lower strength when compared to reinforced plastics. Once the matrix is reinforced with the fibers, the strength properties and elasticity are drastically altered. The overall system becomes high strength under tensile and compressive loads, more suitable for high stress, higher stiffness and will not permanently deform under working load and most importantly resists a broad range of chemicals and is unaffected by moisture making it ideal for application for water immersion systems. Fiber reinforced polymers also have a long life, which may hinder their ability to be recycled, make them great in applications that involve long life systems.
At Protector, majority of our system is constructed using Fibre reinforced polymers , using a distinct ratio of epoxy to fiber that is critical to our systems strength, low weight, durability, long life and corrosion resistance. Several layers are used during construction, included a smooth molded resin rich corrosion barrier inner layer and an external resin rich layer for water penetration resistance.
Specification of orientation of the reinforcing fibers can also increase the strength and resistance to deformation of the polymers. When the fibers are parallel to the direction of force, this is when the fiber reinforced plastic material is at its strongest. This is where the highest strength, stiffness and long life qualities of the system are excelled. However this process can also hinder the material in cases where there is a misalignment of fibers causing shear failure , tensile forces that stretch the matrix more than the fibers can also cause shear failure, in cases where the fiber separates from the matrix causing weaknesses and in cases of extremely high load the fibers themselves can shear. It is hence paramount that during the construction of any FRP system, the engineering and manufacturing processes are up to the highest standards allowing maximum strength.
At PROTECTOR , our fibre reinforced polymer systems are made using a chop hoop filament winding process . Our systems and manufacturing processes ensure that every system has the highest strength and exemplified benefits so that our systems are quality assured and of maximum strength. Protector products are constructed using the advanced chop hoop filament winding process which ensures circumferential as well as longitudinal strength. Every Protector product has a smooth molded resin rich corrosion barrier inner layer and an external resin rich water penetration barrier. Being manufactured in FRP (fiber reinforced plastics) Protector products are light, easy to handle and easy to install. The smooth internal molded finish provides excellent protection against scum build up, exhibit excellent corrosion resistance and are not susceptible to rust.
These material advantages stem from their fiber nature. FRP is hence great for any situations of high stress and high load forces such as an underground installation and infrastructure applications.
They have a high potential to replace conventional materials such as steel and concrete in these infrastructure systems due to their amazing high strength and stiffness, greater fatigue strength and energy absorption capacity and corrosion resistance among other advantages.
Fibre reinforced polymers also have a long life, which may hinder their ability to be recycled, make them great in applications that involve long life systems. The most common industrial uses for Fiber reinforced composites are:
· Windmill blades
· Utility poles
· High posts
· Piping systems
· Underground tank systems
· Engine intake manifolds
· Strengthening in beams, columns, slabs of building structures and bridges -There are three common scenarios where FRP has proven to be more economical than traditional strengthening methods:
· Increases to a structure’s load capacity beyond the original specification or expectation.
· Seismic strengthening
· Repairs to concrete structures that become damaged over time.
In all cases, FRP has less spatial impact on the structure than traditional methods. It is a thin, yet high strength material. This translates into benefits such as not reducing a bridge’s clearance by more than the width of the material (less than 3 millimeters) plus the thin bonding and protective layers.
· Elevator Cables
· Blast Protection
· Marine Systems
All ofProtectors systems are designed and engineered using modern chop hoop filament winding with a chemically resistant interior layer making Protectors systems perfect for use in water systems. With our interior layers and exterior water penetration barriers our Stormwater treatment systems are perfect to deal with any chemical effluent without decay or failure. These systems can be fully immersed, installed underground or in any situation due to the high circumferential and longitudinal strength of our systems.
FRP is such a great material due to a wide range of advantages and benefits.
· Lightweight – FRP is a very lightweight material, at a fraction of the weight of steel or aluminum. Even though it is so lightweight this material is strong enough to withstand the same applied forces and loads due to its amazing strength to weight ratio. As this means that the system will be just as strong and reliable, using a lightweight material will give a plethora of advantages. The system will be much easier to install, often in cases not requiring lifting apparatus. It is sager and simpler to deliver and move and hence will reduce the amount of time spent in installation phase, reducing overall costs dramatically.
· Easy to manufacture – due to the manufacturing processes that are available for Fibre reinforced polymers, almost any shape or configuration is available and hence a wide variety of systems can be manufactured. This means that it has a large sharping versatility and altered with different resins or fibres for various applications. Hence unlike steal or other metal products, it is simple to make complex systems our of FRP and hence the simplicity of manufacturing process allows for a reduction in overall costs for FRP making them the more suitable option for almost all applications.
Our Protector systems are easily manufactured into many shapes, using isotensoidal domes for higher strength in underground installations and internal pressure situations, as well as complex interior shapes and manways. For exampple, our Stormprotector and Hydraprotector systems, our underground oil separator systems have complex dome shapes that are simply made using moulds and complex interior shapes in our ECOPROTECTOR and XTREAMPROTECTOR systems, making what would be difficult manufacture into a simple and speedy process. Furthermore, as their compositions are easily changed additives are simply added to change properties like flame resistant resin additives or temperature additives. This makes these materials easier to design and create for any application, as almost all properties are possible and almost any complex shape is able to be made making it the smart material choice.
· High strength – fibre reinforced polymers have greater flexural strength than timber and gram for gram is a stronger material than steel and aluminum when the fibres are aligned in the force load direction. The fibre additives are able to drastically improve the strength of the material both in tension and in compression making it very applicable to high load situations such as underground installations. Protectors Chop hoop filament winding process ensures that our systems have maximum circumferential and axial strength to allow installation under high loads.
· Corrosion resistance – FRP has a resistance to a wide range of chemical and effluent and is unaffected by moisture of immersion into water making it perfect for applications in marine or chemical circumstances. At protector, we ensure that all of our systems are both corrosion resistant and waterproof. We coat all of our systems with an interior smooth moulded resin rich corrosion barrier as well as an external resin rich water penetration barrier. Unlike steel and aluminium, which are susceptible to oxidation and corrosion, FRP is able to withstand these chemicals and makes it the perfect applications in situations of water storage or treatment.
· High stiffness – FRP is up to 3.3 times as rigid as timber and will not permanently deform under working loads.
· Impact Resistance – Another advantage of Fibre reinforced polymers is that it has high impact resistance, which is that they will never permanently deform or break under impact like traditional building materials. The glass material in the FRP system distributes impact load to prevent surface damage, even in low temperatures.
· Colour – Since fibre reinforced polymer components are moulded, color can be added evenly straight through the part. For more traditional materials, a combination of paints, stains, and coatings must be used and will require periodic re-applications. A wide range of colors are available at Protector, to ensure that the system will aesthetically suit your site.
·Thermal properties – FRP is a great insulator and hence has a low thermal conductivity, unlike metals such as aluminum and steel. Hence this means that fiberglass products maintain a constant temperature and cool to the touch and hence make it a material that is applicable to almost all applications, continuing to operate efficiently at high heat or sub zero temperatures.
· Non-conductive – FRP is a nonconductive material and has a high dielectric capability whilst metals like steel and aluminum conduct electricity readily and must be grounded. This has led to its use in nanotechnology.
· Durability and Long term performance –
· It is considered an Sustainable Product – Sustainable products are products that, through every phase of its life be it construction, manufacture, installation and usage, its energy usage and environmental effect do not go on at a rate that would compromise the natural environment, or that it would not affect the environment negatively over its lifespan. We at Protector put our environments sustainability at the forefront of everything we do. We believe that sustainable energy is the vital to our natural livelihood for future generations. Its manufacturing processes are effective and efficient, minimal wastage in construction, usually does not require more energy that would compromise the natural aspects of its existence and has no environmental harm through the lifespan of its use.
· Cost and Pricing – One of the most important thing when we consider which material to choose is pricing When we compare these two, steel has a lower initial material cost, this is true. But when we consider a wider range of expenses over the life of the system, FRP becomes much more affordable and economically efficient when compared to steel. It has lower installation costs due to its weight, much less maintenance require and a much longer life span all contributing to a cheaper overall cost over time.
It has high strength and is a very reliable material, so why would we replace the modern applications of steel with the Fibre reinforced polymer materials we have available to us to day. Whilst there are many areas in which steel excels as a material, it also has a variety of drawbacks that make in not suitable to some systems, and due to FRPs ability to work with a wide range of additives to change properties.
Steel is very susceptible to corrosion and hence to failure. Oxidation and chemical corrosion are big issues for steel, and hence reduce the amount of applications that steel can be used in, especially in systems with even small risk of exposure. FRP has a resistance to a wide range of chemical and effluent and is unaffected by moisture of immersion into water making it perfect for applications in marine or chemical circumstances. Unlike steel and aluminum, which are susceptible to oxidation and corrosion, FRP is able to withstand these chemicals and makes it the perfect applications in situations of water storage or treatment. Whilst treatment is available to strengthen steel, these treatment processes can sometimes be expensive and reduce the sustainability of steel. The additives to FRP are much simpler and easier to add making it a more cost effective material for applications with corrosion and oxidation risk. Additives to FRP are also able to make its properties alter, adding stronger corrosion resistance, flame retardants and temperature resistance.
Pound to pound, FRP is actually a stronger material than steel, making it a much stronger system whilst maintaining being a very lightweight material. Hence FRP is able to maintain its high strength whilst being a very lightweight material. This means two further advantages of FRP over steel appear.
Firstly FRP systems are much more lightweight than steel making it much easier to install, which has a large amount of time savings and hence cost reduction. The second point is that pound for pound, FRP is actually stronger than steel. This can mean a wide range of advantages in the construction industry, allowing forFRP to be used instead of steel and being able to maintain strength whilst able to reduce weight and also cost. It also hence has a greater strength in tensile and compression as well as in shear due to the addition of fibers for added strength.
Price is probably one of the most important considerations when comparing materials for projects. When we compare these two, steel has a lower initial material cost, this is true. But when we consider a wider range of expenses over the life of the system, FRP becomes much more affordable and economically efficient when compared to steel. It has lower installation costs due to its weight, much less maintenance require and a much longer life span all contributing to a cheaper overall cost over time.
Impact resistance is another property that varies when steel is compared to FRP. FRP as a whole will not permanently deform under a working load. The matrix material distributes impact load to prevent surface damage even in low temperatures whereas steel and other metals such as aluminium deform much easily under working load creating failure where FRP would not.
The other difference between the two is their thermal and electrical conductivity. Steel has high conductivity of both heat and electricity, providing good and bad advantages. FRP however have low thermal conductivity and zero electrical conduction making them perfect for applications where this property is desired. Hence FRP becomes more suitable to more applications in manufacture and construction having the ability to function normally at high temperatures and at sub zero temperatures. With varying thermal energy steel has a much greater fluctuation of its properties, causing it to become more unreliable in varying temperatures, whereas FRP retains its reliability and properties in varying temperature conditions.
Finally when we compare its ease of fabrication and manufacture, a large disparity appears. FRP composites can be field fabricated using a simple carpenters tooling with no welding or torches required. It is also much easier to fabricate into intricate and complex shapes with much greater ease when compared to steel. Steel often requires welding and cutting torches, with the material requiring special equipment to erect and install.
Comparison of FRP with HDPE | ||
Property | FRP | HDPE |
Pricing | Installation cost, maintenance, and cost over life of the system considered less. | Lower initial Cost |
Thermal expansion and contraction | Lower thermal expansion, with 1/10thof the expansion and contraction of HDPE | Higher expansion per degree than FRP |
Operating and Design temperatures | FRPs mechanical properties do not degrade until roughly 83-104.5 | HDPE tends to lose its mechanical properties drastically at 22 degrees. Becomes not recommended when the temperature exceeds 80 degrees. |
Strength | Ultimate Stress = 110MPa | Ultimate Stress = 23MPa |
Pressure Design | Designs at minimum a 6:1 ratio in pressure situations | Lower safety factor in designs causing extreme occasions to be big issue for HDPE |
Fabrication and Installation | Can be manufactured more simply and on site, whereas HDPE requires fabrication in manufacturing plants in complex processes | Can be manufactured to smaller diameters with HDE being quicker to produce |
Modulus of Elasticity | Hoop Modulus = 27.58GPa Axial Modulus = 12.4GPa | HDPE Modulus = 0.69GPa HDPE has higher in ground deflection and pipe bending. Requires piping supports nib some installations |
Weight | Density = 2000 kg/m3 | Density = 970 kg/m3 |
Protector uses exclusively FRP products for every part of our systems. Its high strength and lightweight nature make it the ideal material for construction needs, with complete resistance to chemicals and water immersion
– Protectors FRP systems are ideal for your Stormwater treatment systems.
For many years, Concrete has remained the favorite choice in civil systems due to a wide range of characteristics. Similarly to FRP, concrete is a composite material composed of a fine and coarse aggregate bonded together with a fluid cement that hardens over time. The aggregate is mixed with water and the dry cement, and the mixture forms a slurry which is poured and molded into a variety of shapes. Concrete has a high compression strength, but a low tensile strength, but is able to be reinforced with steel.
But through recent years, Fibre reinforced Polymers have become a material being more and more preferred due to several characteristics.The lightweight property of FRP gives it several beneficial aspects when considered against concrete. The first benefit of lightweight materials is the reduced installation and transport costs. With rising transportation costs and construction costs, a quick and simple installation can save a drastic amount of money.
FRP materials are also much easier for installation as the processes are simple and this ease of manufacture on site allows for simple tooling to create and adjust parts on site. When considering bridge constructions, specifically bridge deck panels, FRP are easier in transport and faster to install. Furthermore concrete requires 28 days to cure and precast concrete panels require heavy duty equipment, again providing further savings. FRP also requires much less substructure (ground connections) and much less superstructure requiring a lower overall cost than concrete.
Coloring is another great example of change. Concrete cannot be changed in color without much difficulty and specialty products. FRP on the other hand can be easily pigmented and color at any stage of manufacture. This allows FRP systems to blend into any environment and can provide more aesthetic options.
A major point of the differences between the two systems is the variation in corrosion and decay of both systems. Concrete has a lot of weaknesses which in certain applications can become dangers to concrete structures. When concrete is exposed to a range of chemicals or water, issues may arise. Concrete is more susceptible to corrosion and decay, and is not recommended in systems that are exposed to salt water such as coastal areas. FRP is highly chemical resistant. It is highly resistant to water, salt, and chemicals, hot and cold temperature extremes ad variables found in coastal environments. At PROTECTOR, we use a smooth interior corrosion layer and external water penetration barrier to ensure our systems are chemically resistant and watertight. It is this that has led FRP to become favorable in construction and civil exercises, with the outer layers being and FRP material to be resistance to weathering and corrosion. Furthermore, FRP is considered an extremely water tight system, with its concrete being porous and can form leaks. Hence in water effluent systems, FRP is a much more preferred material.
As a further point, concrete has a lifespan on anywhere between 15 to 50 years, depending on the environment – in environments with salt and coastal weather patterns even less! FRP however has an expected lifespan of over 75 years, range to up to 150 years.
PROTECTOR’s products are designed with a 6:1 design factor of safety and designed for the longest life possible, aiming for a 150-year for all products. The lifespan alone will dramatically reduce lifetime costs, with less replacement of systems and maintenance than for FRP systems. FRP systems also have the advantage of having no degradation over time, with concrete having decay and damage over time causing sooner replacement when considered against FRP.
In fabrication concrete tanks are built in sections requiring field assembly. Each joint is a potential leak even with additional sealants. Fiberglass tanks are monolithic. FRP is easier to assemble, with even the possibility of fabrication and manufacture on site with simple tools, or more commonly having a preassembled system if possible. Furthermore in terms of maintenance fiberglass is much easier to clean and keep clean, extending the life of the interior parts such as pumping systems and valves.
When we consider them as systems built for underground tanks, similar to what Protector does with its stormwater treatment systems, we see some major disparity.
FRP vs Concrete in Underground Tank and Water Treatment Systems | ||
PROPERTY | FRP | CONCRETE |
Water Resistance and Leakages | FRP systems
are water-tight and Protectors systems have an external resin-rich water-tight penetration barrier. |
Concrete is a porous material allowing water to penetrate the
surface. Even with sealants concrete can leak |
Structural strength | Strong material in terms of strength, will not degrade over time | Degrades over time, although initial strength of the system is greater |
Lifespan | 75 year guaranteed lifetime, up to 150 years max | Between 15-50 years expected lifespan |
Fabrication | FRP systems can be made as a whole, monolithic system with no leaks usually coming pre-assembled. | Concrete must be built as separate sections for ease of delivery and installation, hence joints provides weaknesses even with additional sealants. More complex systems are required in the manufacture of concrete assemblies. |
Expansion and contraction | Fiberglass has a low coefficient of expansion under heat and weather conditions. | Concrete expands and contracts regularly with temperate cause cracks to appear and corrosion. |
Corrosion due to Microbial Induced Corrosion | Resistance to all chemical corrosion types | Hydrogen supplied creates sulphuric acid when in underground water systems, a common cause of deterioration of concrete. |
Bacteria resistance | FRP products at Protector are manufactured with smooth interior resistant layers and exterior waterproof layers making it perfect environment to combat bacteria and algae accumulation. | Not suitable |
Oxidation resistance | Is not effected by Oxidation | Concrete often uses steel rebar for reinforcement and the rebar is susceptible to rust from water permeating the surface. |
Weight | Lightweight requiring smaller crane systems for loading and offloading. Weighs approx. 1400kg per cubic m | Concrete is a heavier system. Weights approx 2400kg per cub meter. |
Installation | Fiberglass tanks can be transported on a single truck and are delivered to the site as a finished product making installation easier and faster | Requires step by step installation on site as concrete systems have to be poured and set. Requires more transportation increasing time and expenses. |
Maintenance and Repairs | Additional appurtenances can be installed directly to the FRP tank at the job site and even after burial. Fiberglass does not require resurfacing for the life of the product. Fiberglass is easier to clean and keep clean which extends the life of pumps and filtering equipment. | Much more difficult in all stages of maintenance to deal with, more difficult to clean and maintain requiring higher frequency and increased cost over the life of the system. |
Stormwater Management is the method of collection and treatment of stormwater so that it can be utilized for our day to day activities. Therefore, managing the quantity and quality of stormwater is called Stormwater Management. Effective stormwater management techniques aim at trapping the highest amounts of stormwater and effective treatment of the stormwater via the treatment train, thereby making most of the stormwater useful for us.
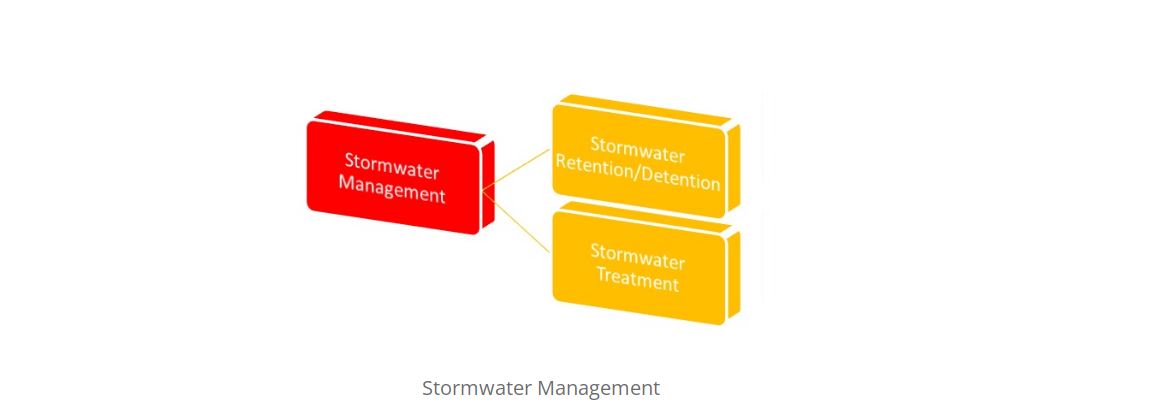
Due to the spraying of pesticides and fertilizers on the agricultural fields, these fields tend to have a high concentration of nutrients like nitrogen and phosphorous. The stormwater on contact with these fields and can have a very high concentration of nutrients. This nutrient-rich stormwater can be very troublesome downstream to the receiving waterbody and can lead to eutrophication, which can, in turn, affect the marine ecosystem and aquatic life within that system. Therefore, nutrient removal from stormwater can be very vital for the marine ecosystem balance to be maintained.
Stormwater nutrient removal is a part of tertiary treatment which is the final stage of treatment train. Therefore, it is one of the last safeguards for treating stormwater before it enters waterways.
The stormwater nutrient removal can either be done with the utilization of proprietary treatment devices (a filter or a combination of filters) that can absorb these nutrients or a biofilter can be designed to remove the nutrients to the desired standard limits or the limits set by the guidelines. Various materials have been studied and utilized as filters for nutrient removal in the past, like sand and soil-based water filter, high flow media etc. These proprietary treatment devices can be very effective for the removal in areas with a shortage of land since biofilters require large areas.
Enquire with us
Today!
Call 1300 585 787